Ever Safe Homes: Pioneering Resilient and Sustainable Living Through Innovative Building Systems
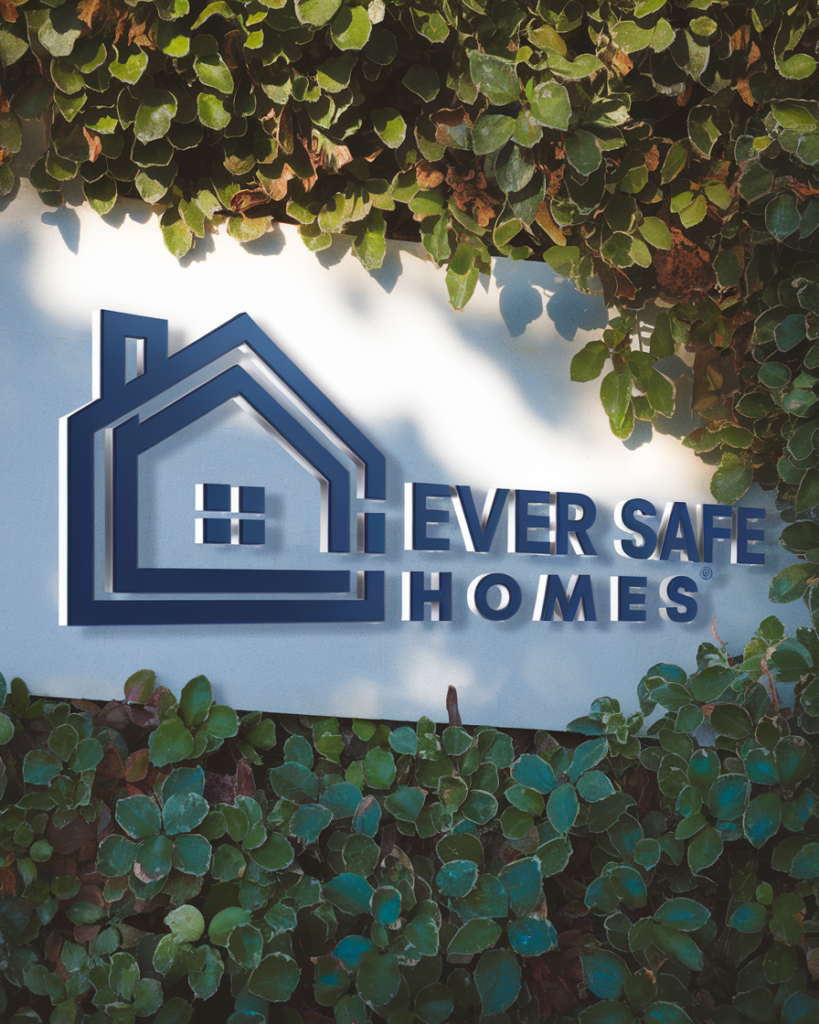
Introducing Ever Safe Homes
At Ever Safe Homes, we’re redefining the future of home construction. By seamlessly integrating Insulated Concrete Forms (ICF), RSG 3-D Structural Concrete Insulated Panels (SCIP), Starcell SpA’s honeycomb technology, and steel framing, we create homes that are stronger, more energy-efficient, and perfectly tailored to modern living.
Why Choose Ever Safe Homes?
1. Unparalleled Structural Strength and Safety
- Disaster-Resistant Construction: Our homes are engineered to withstand earthquakes, hurricanes, fires, and other extreme weather events. The fusion of ICF, RSG 3-D SCIP, and steel framing ensures exceptional structural integrity.
- RSG 3-D Structural Concrete Insulated Panels (SCIP): RSG 3-D’s SCIP system combines a three-dimensional welded wire space frame, an expanded polystyrene insulation core, and layers of shotcrete (concrete). This creates a monolithic structure that offers outstanding strength, durability, and thermal efficiency.
2. Superior Energy Efficiency
- Thermal Insulation Excellence: The combination of ICF and RSG 3-D SCIP creates a highly efficient thermal envelope, maintaining comfortable indoor temperatures year-round.
- Reduced Energy Costs: Enjoy significant savings on heating and cooling bills due to the enhanced insulation properties of our integrated building systems.
3. Innovative Design and Aesthetics

- Starcell’s Honeycomb Technology: Our use of Starcell’s lightweight yet strong honeycomb panels allows for creative and versatile architectural designs without compromising structural integrity.
- Customization: Our design team collaborates with you to create a home that reflects your personal style and meets your functional needs.
4. Efficient and Precise Construction
- Streamlined Construction Process: By utilizing prefabricated components like RSG 3-D SCIP and ICF, we reduce construction time and minimize on-site labor costs.
- Quality Assurance: Off-site manufacturing in controlled environments ensures each component meets our stringent quality standards before arriving at your build site.
5. Commitment to Sustainability
- Eco-Friendly Materials: We prioritize the use of recyclable and sustainable materials, reducing the environmental impact of your home.
- Reduced Waste: Precision engineering and prefabrication lead to minimal material waste during construction.
Our Integrated Building System Components
Insulated Concrete Forms (ICF)
- Energy Efficiency: ICF provides continuous insulation, enhancing thermal performance and reducing energy consumption.
- Strength and Durability: ICF walls offer excellent resistance to fire, moisture, and sound, contributing to a safer and more comfortable home.
RSG 3-D Structural Concrete Insulated Panels (SCIP)
- Exceptional Structural Integrity: RSG 3-D’s SCIP system creates walls and roofs that are monolithic, providing unmatched strength and resilience.
- Thermal Performance: The expanded polystyrene core offers excellent insulation, reducing energy costs and enhancing indoor comfort.
- Versatility: Suitable for a variety of architectural designs, allowing for flexibility in creating unique and personalized homes.
Starcell SpA Honeycomb Technology
- Lightweight and Strong: Starcell’s honeycomb panels offer a high strength-to-weight ratio, enabling innovative designs without sacrificing structural integrity.
- Aesthetic Versatility: Ideal for both interior and exterior applications, allowing for customized finishes and design elements.
Steel Framing
- Precision and Stability: Steel provides a durable framework that is resistant to pests, fire, and rot.
- Sustainability: Steel is highly recyclable, supporting environmentally responsible construction practices.
Experience the Ever Safe Difference
Homes Built for Safety and Longevity
Your home is more than just a building; it’s a sanctuary for you and your family. At Ever Safe Homes, we prioritize:
- Safety: Our integrated building systems ensure your home is built to withstand the tests of time and nature.
- Comfort: Benefit from superior thermal and sound insulation, creating a peaceful living environment.
- Value: Invest in a home that offers long-term savings, durability, and enhanced resale value.
Personalized Service
We are dedicated to providing an exceptional customer experience:
- Collaborative Design Process: Partner with our architects and designers to bring your vision to life.
- Transparent Communication: Stay informed and engaged throughout every stage of construction.
- Continued Support: Our commitment to you extends beyond completion—we’re here to assist you for years to come.
Join the Ever Safe Homes Community
Imagine living in a home that offers security, efficiency, and style—all while being environmentally conscious. With Ever Safe Homes, this ideal becomes your reality.
Ideal For:
- Families Prioritizing Safety and Comfort
- Eco-Conscious Homeowners Seeking Sustainability
- Investors Looking for Quality and Long-Term Value
- Anyone Ready to Embrace Innovative Living Spaces
Ever Safe Homes—Building a Safer, Sustainable Future
Choose Ever Safe Homes and invest in a home that’s designed for the future. Together, we’ll build not just a house, but a legacy of safety, innovation, and environmental stewardship.
Ever Safe Homes—where innovation meets peace of mind.
Comprehensive Integration of Ever Safe Homes, Safe Space Modular, Haven Craft Design, Resilience ADU, RSG 3-D, and Starcell SpA: A Unified Approach to Innovative and Sustainable Construction
Introduction
The collaboration between Ever Safe Homes, Safe Space Modular, Haven Craft Design, Resilience ADU, RSG 3-D, and Starcell SpA represents a groundbreaking synergy in the construction industry. By combining advanced materials, innovative design, and modular construction techniques, this alliance offers resilient, sustainable, and customizable building solutions for residential, commercial, and industrial applications.
This integrated approach leverages the strengths of each entity to deliver high-quality structures that meet the evolving needs of clients while promoting environmental responsibility.
1. Ever Safe Homes: The Retail Home Builder
Role in the Collaboration
- Customer Interface: Ever Safe Homes serves as the primary retail home builder, bringing the collaborative products and services directly to consumers.
- Project Management: They oversee the construction process from inception to completion, ensuring that projects are delivered on time and within budget.
- Quality Assurance: Committed to excellence, Ever Safe Homes ensures that all structures meet stringent quality standards and comply with building codes.
Integration with Other Partners
- Design Implementation: Works closely with Haven Craft Design to translate architectural visions into reality.
- Material Utilization: Incorporates advanced materials from RSG 3-D and Starcell SpA into their building projects.
- Modular Solutions: Utilizes Safe Space Modular’s prefabricated components for efficient construction.
2. Haven Craft Design: Architectural Innovation
Role in the Collaboration
- Architectural Design: Provides bespoke design services that prioritize aesthetics, functionality, and sustainability.
- Customization: Tailors designs to meet individual client preferences and site-specific requirements.
Integration with Other Partners
- Material Selection: Specifies the use of RSG 3-D and Starcell SpA products to achieve desired structural and aesthetic outcomes.
- Collaboration with Ever Safe Homes: Ensures that designs are feasible and align with construction capabilities.
- Support for ADUs: Works with Resilience ADU to design versatile accessory dwelling units that complement main structures.
3. Safe Space Modular: Modular Construction Excellence
Role in the Collaboration
- Modular Solutions: Specializes in creating prefabricated modules for deployable data centers, ADUs, and other structures.
- Rapid Deployment: Focuses on efficient assembly and disassembly processes to reduce construction time.
Integration with Other Partners
- Materials Integration: Utilizes Starcell SpA’s honeycomb panels for lightweight and strong modular components.
- Collaboration with Ever Safe Homes: Supplies modular units for residential and commercial projects.
- Design Alignment: Works with Haven Craft Design to ensure modular components meet design specifications.
4. Resilience ADU: Sustainable Accessory Dwelling Units
Role in the Collaboration
- ADU Expertise: Develops accessory dwelling units that are sustainable, efficient, and versatile.
- Regulatory Compliance: Ensures that all ADUs meet local zoning laws and building regulations.
Integration with Other Partners
- Material Use: Incorporates RSG 3-D and Starcell SpA products for enhanced durability and energy efficiency.
- Sales and Installation: Partners with Ever Safe Homes for the retailing and installation of ADUs.
- Design Collaboration: Aligns with Haven Craft Design to create ADUs that complement primary residences.
5. RSG 3-D: Advanced Structural Panels
Role in the Collaboration
- Innovative Materials: Produces high-performance structural panels with superior strength and insulation properties.
- Energy Efficiency: Contributes to the construction of buildings with lower energy consumption.
Integration with Other Partners
- Material Supply: Provides panels to Ever Safe Homes, Safe Space Modular, and Resilience ADU.
- Design Support: Works with Haven Craft Design to optimize the use of panels in architectural plans.
- Construction Synergy: Enhances the structural integrity of modular units and ADUs.
6. Starcell SpA: Honeycomb Panel Technology
Role in the Collaboration
- Advanced Materials: Offers honeycomb panels that are lightweight yet exceptionally strong.
- Versatility: Supplies materials suitable for a variety of applications, from walls to flooring.
Integration with Other Partners
- Material Integration: Panels are used by Safe Space Modular for modular units and by Ever Safe Homes in traditional construction.
- Design Flexibility: Enables Haven Craft Design to explore innovative architectural solutions.
- Enhanced Durability: Improves the resilience of structures built by Ever Safe Homes and Resilience ADU.
7. Cohesive Collaboration and Complementary Cohesion
A. Unified Vision and Goals
- Innovation: All partners are committed to pushing the boundaries of construction technology.
- Sustainability: A shared focus on eco-friendly materials and energy-efficient designs.
- Quality and Resilience: Delivering structures that are built to last and withstand environmental challenges.
B. Streamlined Processes
- Integrated Supply Chain: Efficient coordination between material suppliers (RSG 3-D and Starcell SpA) and builders (Ever Safe Homes and Safe Space Modular).
- Collaborative Design: Ongoing communication between Haven Craft Design and other partners to ensure design feasibility and aesthetic harmony.
- Customer-Centric Approach: Ever Safe Homes provides a single point of contact for clients, simplifying the construction process.
C. Diverse Applications
- Residential Homes: Custom-built homes that leverage modular components and advanced materials for superior performance.
- ADUs and Extensions: Flexible solutions for additional living spaces, home offices, or rental units.
- Commercial Structures: Office buildings, retail spaces, and data centers that benefit from modular construction and innovative materials.
- Emergency and Remote Deployments: Rapidly deployable units for disaster relief, military, or remote industrial operations.
8. Benefits of the Integrated Approach
Enhanced Efficiency
- Reduced Construction Time: Prefabricated modules and streamlined processes accelerate project completion.
- Cost Savings: Efficient use of materials and labor reduces overall project costs.
Superior Quality
- High-Performance Materials: Use of RSG 3-D and Starcell SpA products ensures durability and longevity.
- Quality Control: Prefabrication allows for rigorous quality checks before components reach the construction site.
Sustainability
- Eco-Friendly Materials: Commitment to using recyclable and sustainable materials minimizes environmental impact.
- Energy Efficiency: Improved insulation and building systems reduce energy consumption.
Customization and Flexibility
- Tailored Designs: Haven Craft Design offers personalized architectural solutions.
- Scalability: Modular construction allows for easy expansion or modification of structures.
9. The Role of Each Partner in the Customer Journey
Initial Consultation
- Ever Safe Homes meets with clients to understand their needs and introduce the collaborative capabilities.
- Haven Craft Design engages to develop initial design concepts.
Design and Planning
- Haven Craft Design creates detailed architectural plans.
- Material Suppliers (RSG 3-D and Starcell SpA) provide specifications to optimize material use.
- Safe Space Modular offers modular solutions where applicable.
Construction
- Ever Safe Homes manages on-site construction, coordinating the delivery and assembly of materials and modules.
- Resilience ADU installs ADUs as part of the project when required.
Completion and Aftercare
- Ever Safe Homes conducts final inspections and ensures client satisfaction.
- All Partners remain available for maintenance, upgrades, and future expansions.
10. Conclusion
The integration of Ever Safe Homes, Safe Space Modular, Haven Craft Design, Resilience ADU, RSG 3-D, and Starcell SpA forms a cohesive and comprehensive construction solution. This collaboration harnesses the strengths of each partner to deliver:
- Innovative Designs: Architectural excellence that meets modern aesthetic and functional demands.
- Advanced Materials: Cutting-edge products that enhance building performance and longevity.
- Efficient Construction: Modular methods that reduce build times and costs.
- Sustainable Practices: Environmentally responsible approaches that benefit both clients and the planet.
By choosing this integrated solution, clients gain access to a seamless construction experience that delivers high-quality, customized structures designed to meet their unique needs.
By uniting their expertise and resources, these companies are redefining the construction landscape, offering solutions that are not only efficient and resilient but also tailored to the aspirations of modern living and working spaces.
Incorporating Insulated Concrete Forms (ICF) and Structural Concrete Insulated Panels (SCIP) into the Construction Process: Benefits and Synergies
Introduction
Combining Insulated Concrete Forms (ICF) and Structural Concrete Insulated Panels (SCIP) in your construction process can significantly enhance the overall quality, efficiency, and performance of your building projects. Both ICF and SCIP are innovative building systems that offer superior insulation, structural strength, and energy efficiency. Integrating these systems can lead to a construction process that is faster, more cost-effective, and results in structures that are robust, sustainable, and comfortable.
Understanding ICF and SCIP
1. Insulated Concrete Forms (ICF)
- Description: ICF systems consist of hollow blocks or panels made of insulating foam (usually expanded polystyrene) that are stacked to form the shape of walls. Once assembled, concrete is poured into the hollow centers, creating a solid, reinforced concrete wall with continuous insulation on both sides.
- Benefits:
- Energy Efficiency: Provides excellent thermal insulation, reducing heating and cooling costs.
- Structural Strength: Reinforced concrete offers high durability and resistance to natural disasters.
- Sound Insulation: Superior sound-dampening properties for a quieter indoor environment.
- Fire Resistance: Concrete and foam materials used in ICF are non-combustible.
- Moisture Control: Reduced risk of mold and mildew due to moisture-resistant materials.
2. Structural Concrete Insulated Panels (SCIP)
- Description: SCIP, also known as 3D panels or sandwich panels, consist of a polystyrene foam core sandwiched between two layers of welded wire mesh. These panels are assembled on-site and then coated with shotcrete (sprayed concrete), creating a monolithic, insulated concrete structure.
- Benefits:
- Structural Integrity: The combination of concrete and steel mesh provides exceptional strength.
- Thermal Performance: The foam core offers continuous insulation, enhancing energy efficiency.
- Versatility: Can be used for walls, roofs, floors, and even complex architectural shapes.
- Speed of Construction: Lightweight panels are easy to handle and install, accelerating the building process.
- Seismic and Wind Resistance: Monolithic construction offers superior performance in seismic zones and high-wind areas.
Benefits of Incorporating ICF and SCIP
1. Enhanced Structural Strength and Resilience
- Synergistic Strength: Combining ICF’s reinforced concrete core with SCIP’s monolithic panel system results in a structure with outstanding load-bearing capacity and structural integrity.
- Disaster Resistance: The integration provides enhanced protection against earthquakes, hurricanes, floods, and fires, ensuring occupant safety and reducing potential damage.
2. Superior Energy Efficiency
- Continuous Insulation: Both systems provide uninterrupted insulation layers, minimizing thermal bridging and maintaining consistent indoor temperatures.
- Reduced Energy Costs: Enhanced thermal performance leads to significant savings on heating and cooling expenses over the building’s lifespan.
- Comfortable Living Spaces: Improved insulation contributes to better humidity control and overall indoor comfort.
3. Improved Construction Efficiency
- Faster Build Times: Prefabricated components and straightforward assembly processes reduce construction schedules.
- Labor Savings: Ease of installation reduces the need for specialized labor, lowering overall construction costs.
- Weather Resilience During Construction: Both systems allow for building in various weather conditions, minimizing delays.
4. Design Flexibility
- Architectural Versatility: SCIP panels can accommodate curved walls, arches, and unique architectural features, while ICF allows for various wall thicknesses and finishes.
- Integration with Other Systems: Both ICF and SCIP can be combined with other building materials, such as steel framing and Starcell’s honeycomb panels, for customized solutions.
5. Sustainability and Environmental Benefits
- Reduced Waste: Precise manufacturing and installation processes lead to less material waste on-site.
- Lower Carbon Footprint: Energy-efficient buildings reduce greenhouse gas emissions associated with heating and cooling.
- Recyclable Materials: Many components used in ICF and SCIP systems are recyclable, promoting environmental responsibility.
How to Incorporate ICF and SCIP into Your Construction Process
1. Strategic Planning and Design
- Assess Project Requirements: Determine the specific needs of your project, including structural demands, architectural design, and energy efficiency goals.
- Hybrid Approach: Use ICF for below-grade walls and foundations where moisture resistance and thermal mass are beneficial, and SCIP for above-grade walls and roofs to take advantage of their lightweight and versatile design.
- Collaborate with Professionals: Work with architects and engineers experienced in both systems to optimize the design for performance and cost-effectiveness.
2. Material Selection and Procurement
- Quality Materials: Source high-quality ICF blocks and SCIP panels to ensure durability and performance.
- Supplier Relationships: Establish partnerships with reputable manufacturers for consistent supply and technical support.
3. Training and Workforce Development
- Skilled Installation: Provide training for construction crews on the specific techniques required for ICF and SCIP installation.
- Safety Protocols: Emphasize safety practices, especially when working with concrete pouring and shotcrete application.
4. Integration with Other Systems
- Combine with Steel Framing: Use steel framing in conjunction with SCIP for additional structural support where needed.
- Incorporate Starcell’s Honeycomb Panels: For interior partitions and non-load-bearing walls, utilize Starcell’s panels for lightweight, durable solutions.
5. Construction Process Optimization
- Site Preparation: Ensure the building site is properly prepared for the efficient installation of ICF and SCIP systems.
- Sequencing: Plan the construction sequence to maximize efficiency, such as erecting SCIP walls while ICF foundations cure.
- Quality Control: Implement regular inspections to verify that installation meets design specifications and manufacturer guidelines.
Potential Challenges and Solutions
1. Initial Costs
- Challenge: Upfront costs for ICF and SCIP materials may be higher than traditional construction methods.
- Solution: Emphasize long-term savings from energy efficiency, reduced maintenance, and faster construction times. Seek volume discounts from suppliers.
2. Availability of Skilled Labor
- Challenge: Finding workers experienced with ICF and SCIP may be difficult in some regions.
- Solution: Invest in training programs and partner with manufacturers who offer installation support and certification.
3. Building Code Compliance
- Challenge: Navigating local building codes and obtaining approvals for alternative construction methods.
- Solution: Engage early with local building authorities, provide detailed plans and engineering reports, and demonstrate compliance with relevant standards.
Case Studies and Applications
Residential Projects
- Custom Homes: Builders have successfully used ICF for basements and SCIP for above-ground walls, creating energy-efficient homes with unique architectural features.
- Multi-Family Housing: Developers have utilized the speed of SCIP construction to reduce project timelines and costs in apartment buildings.
Commercial Buildings
- Office Spaces: Combining ICF foundations with SCIP walls offers durable and energy-efficient commercial structures.
- Educational Facilities: Schools have benefited from the safety and energy savings provided by these systems.
Disaster-Resilient Structures
- Emergency Shelters: The rapid construction and robustness of ICF and SCIP make them ideal for building shelters in disaster-prone areas.
- Military Installations: Governments have adopted these systems for secure and durable facilities.
Conclusion
Incorporating both Insulated Concrete Forms (ICF) and Structural Concrete Insulated Panels (SCIP) into your construction process offers a multitude of benefits that enhance the quality and performance of your projects. The synergy between these two systems can lead to:
- Stronger Structures: Enhanced resistance to natural disasters and increased longevity.
- Energy Efficiency: Significant reductions in energy consumption and costs.
- Faster Construction: Accelerated building schedules and earlier project completion.
- Design Flexibility: The ability to create unique and innovative architectural designs.
- Sustainability: Reduced environmental impact through energy savings and the use of recyclable materials.
By integrating ICF and SCIP, you position your construction projects at the forefront of modern building technology, delivering superior value to clients and setting new standards in the industry.